In recent years, with the revival of the construction machinery and wind power industries, large-scale slewing bearings and shaft gears have seen rapid development. However, a common quality issue remains: the quenching of the tooth profile often fails to meet design specifications. This leads to uneven wear during operation, significantly reducing the service life of these critical components.
After thorough analysis, the main cause was identified as inaccurate indexing due to mechanical or other factors during the process. Because these parts have a high number of teeth and a large module, the gap between the induction heating device and the tooth profile is not always consistent. As a result, the heating becomes uneven, leading to inconsistent hardness on both sides of the teeth after quenching, which ultimately causes uneven wear.
To address this challenge, Shiyan Gaozhoubo Industry and Trade Co., Ltd. initiated a technical research project and eventually introduced an automatic tooth profile tracking and positioning system (see Figure 1).
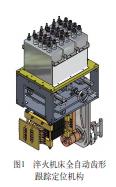
The system consists of a floating two-dimensional sliding table, a quenching transformer, a sensor transition row, a sensor rotating mechanism (see Figure 2), a quenching sensor, and a tooth shape tracking and positioning mechanism.
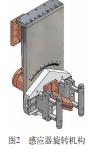
The floating two-dimensional sliding table features guiding mechanisms in the X and Y directions, along with return springs on the guide columns. It automatically adjusts its position based on external forces and resets when those forces are removed. The quenching transformer and transitional row provide the necessary energy for induction hardening, while the sensor rotating mechanism is specifically designed to handle helical gear tracking. The tooth shape tracking and positioning mechanism uses two cylinders to adjust front and back, left and right positions, ensuring the sensor remains in the correct location for straight teeth. For helical teeth, two balls are used as a positioning mechanism to keep the sensor fixed.
The working principle of the quenching machine involves positioning and clamping the slewing bearing or pinion on the indexing rotary table. The machine slide moves to the tooth position, where the sensor and tooth profile are manually adjusted. The gap between the teeth and the tracking mechanism is aligned with adjacent tooth profiles. Once the heating power supply is activated, continuous heating of the tooth profile begins. After each tooth is heated and quenched via the indexing turntable, the sensor automatically tracks into the next tooth, eliminating the need for manual gap adjustments and improving the efficiency of the induction hardening process.
To ensure compatibility with both helical and herringbone teeth, the sensor connection mechanism is designed to be rotatable. The induction quenching process for helical teeth is similar to that of straight teeth, but it requires three-axis servo linkage during heating. Technical specifications include a ±30mm float range on the two-dimensional sliding table and a helical angle of ±35° for helical teeth.
Through these improvements, the mechanism now fully meets customer requirements, enhances product quality, ensures uniform quenching, and stabilizes the metallographic structure.
Classic Composite Decking,Wood Plastic Composite Decking,Composite Wood Decking,Wood Plastic Composite
Jinhu Jusheng Plastic Wood New Material Co.,Ltd , https://www.goldenlakewpc.com